Các bộ phận kim loại chính xác thường được sản xuất bằng nhiều công nghệ gia công chính xác khác nhau, trong đó gia công CNC là phương pháp phổ biến. Thông thường, các bộ phận chính xác thường đòi hỏi tiêu chuẩn cao về cả kích thước và hình thức.
Do đó, khi sử dụng gia công CNC các kim loại như nhôm và đồng, việc xuất hiện các vết và đường của dụng cụ trên bề mặt thành phẩm là một mối quan tâm. Bài viết này thảo luận về các lý do gây ra các vết và đường của dụng cụ trong quá trình gia công các sản phẩm kim loại. Chúng tôi cũng đề xuất các giải pháp tiềm năng.
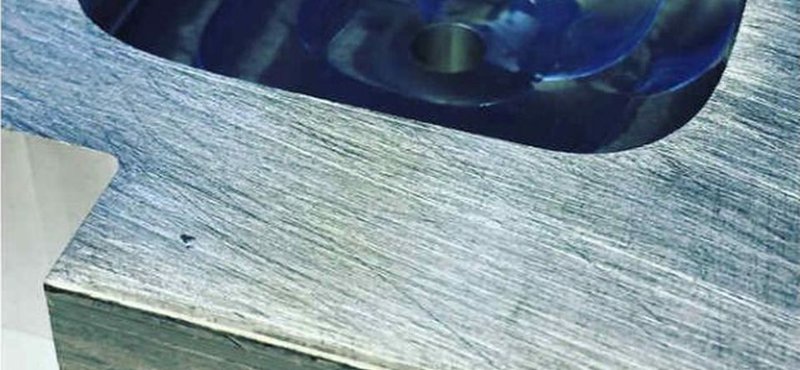
Lực kẹp của đồ gá không đủ
Nguyên nhân:Một số sản phẩm kim loại rỗng cần sử dụng thiết bị cố định chân không và có thể khó tạo đủ lực hút do bề mặt không bằng phẳng, tạo ra vết hoặc đường rãnh do dụng cụ.
Giải pháp:Để giảm thiểu điều này, hãy cân nhắc chuyển từ hút chân không đơn giản sang hút chân không kết hợp với áp suất hoặc hỗ trợ bên. Ngoài ra, hãy khám phá các tùy chọn đồ gá thay thế dựa trên cấu trúc bộ phận cụ thể, điều chỉnh giải pháp cho vấn đề cụ thể.
Các yếu tố liên quan đến quy trình
Nguyên nhân:Một số quy trình sản xuất sản phẩm có thể góp phần gây ra vấn đề. Ví dụ, các sản phẩm như vỏ sau máy tính bảng trải qua một chuỗi các bước gia công bao gồm đục lỗ bên hông sau đó là phay CNC các cạnh. Chuỗi này có thể dẫn đến các vết dụng cụ đáng chú ý khi phay đến các vị trí lỗ bên hông.
Giải pháp:Một trường hợp phổ biến của vấn đề này xảy ra khi hợp kim nhôm được chọn cho vỏ sản phẩm điện tử. Để giải quyết, quy trình có thể được sửa đổi bằng cách thay thế đục lỗ bên cộng với phay bằng phay CNC. Đồng thời, đảm bảo sự ăn khớp nhất quán của dụng cụ và giảm cắt không đều khi phay.
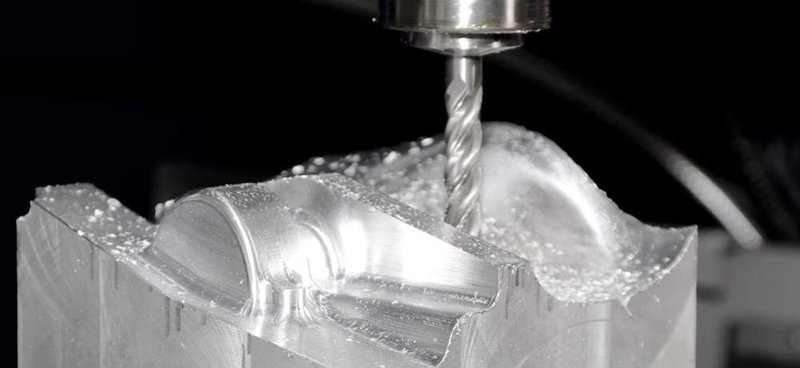
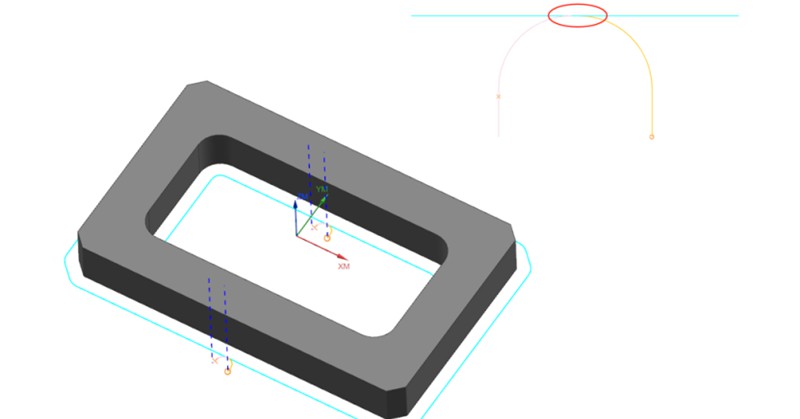
Lập trình không đầy đủ về sự tham gia của đường dẫn công cụ
Nguyên nhân:Vấn đề này thường phát sinh trong giai đoạn gia công đường viền 2D của quá trình sản xuất sản phẩm. Đường chạy dao được thiết kế kém trong chương trình CNC, để lại dấu vết tại điểm vào và ra của dao.
Giải pháp:Để giải quyết thách thức tránh vết dụng cụ tại điểm vào và điểm ra, một cách tiếp cận thông thường là tạo ra một khoảng chồng chéo nhỏ trong khoảng cách tiếp xúc của dụng cụ (khoảng 0,2mm). Kỹ thuật này giúp tránh được những sai sót tiềm ẩn trong độ chính xác của vít dẫn của máy.
Mặc dù chiến lược này ngăn ngừa hiệu quả việc hình thành vết dụng cụ, nhưng nó lại gây ra yếu tố gia công lặp đi lặp lại khi vật liệu của sản phẩm là kim loại mềm. Do đó, phần này có thể biểu hiện sự khác biệt về kết cấu và màu sắc so với các khu vực khác.
Các mẫu vảy cá trên bề mặt gia công phẳng
Nguyên nhân:Các mẫu hình vảy cá hoặc hình tròn xuất hiện trên bề mặt phẳng của sản phẩm. Các dụng cụ cắt được sử dụng để gia công kim loại mềm như nhôm/đồng thường là máy phay vật liệu hợp kim có 3 đến 4 rãnh. Chúng có độ cứng từ HRC55 đến HRC65. Các dụng cụ cắt phay này được thực hiện bằng cách sử dụng cạnh dưới của dụng cụ và bề mặt chi tiết có thể phát triển các mẫu hình vảy cá đặc biệt, ảnh hưởng đến hình thức tổng thể của chi tiết.
Giải pháp:Thường thấy ở các sản phẩm có yêu cầu về độ phẳng cao và bề mặt phẳng có cấu trúc lõm. Một biện pháp khắc phục là chuyển sang sử dụng các dụng cụ cắt làm từ vật liệu kim cương tổng hợp, giúp đạt được bề mặt hoàn thiện mịn hơn.
Lão hóa và hao mòn của các thành phần thiết bị
Nguyên nhân:Vết công cụ trên bề mặt sản phẩm là do sự lão hóa và hao mòn của trục chính, ổ trục và vít dẫn của thiết bị. Ngoài ra, các thông số độ rơ của hệ thống CNC không phù hợp góp phần tạo ra vết công cụ rõ rệt, đặc biệt là khi gia công các góc bo tròn.
Giải pháp:Những vấn đề này xuất phát từ các yếu tố liên quan đến thiết bị và có thể được giải quyết bằng cách bảo trì và thay thế có mục tiêu.
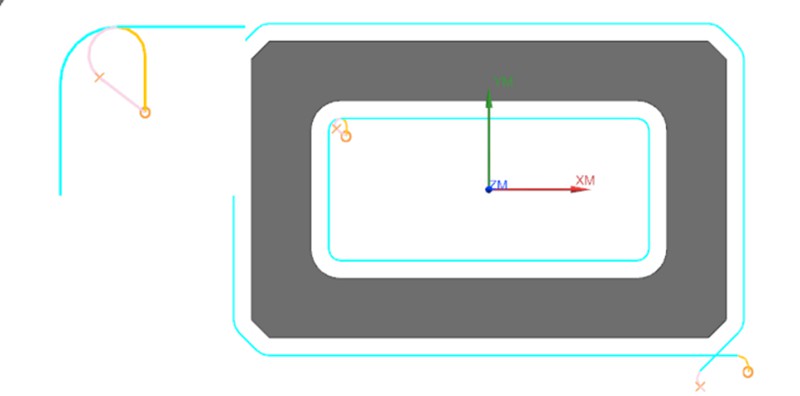
Phần kết luận
Để đạt được bề mặt lý tưởng trong kim loại gia công CNC đòi hỏi những cách tiếp cận hữu ích. Có nhiều phương pháp khác nhau để tránh các vết và đường của dụng cụ liên quan đến sự kết hợp giữa bảo trì thiết bị, cải tiến đồ gá, điều chỉnh quy trình và tinh chỉnh lập trình. Bằng cách hiểu và khắc phục các yếu tố này, các nhà sản xuất có thể đảm bảo rằng các thành phần chính xác không chỉ đáp ứng các tiêu chí về kích thước mà còn thể hiện các phẩm chất thẩm mỹ mong muốn.